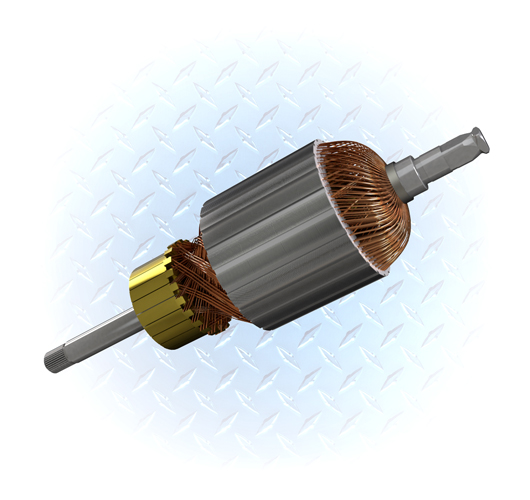
BTI engineers and manufactures a complete line of manual, semi-automatic, and fully automatic precision measurement and testing equipment for all armature, rotor, and motor assemblies, as well as related assemblies and components
BTI engineers and manufactures a complete line of manual, semi-automatic, and fully automatic precision measurement and testing equipment for all armature, rotor, and motor assemblies, as well as related assemblies and components. Traditional equipment types for armatures and rotors include balancing and high-pot testing with production rates varying from 60 to 600 parts per hour. Traditional motor assembly equipment includes balancing, bearing health, vibration, temperature, product assembly with force and distance confirmation, current vs. speed, airflow, blade counting, blade direction, noise, axial and radial run out, current draw, and NVH. Typical balance correction methods for motor assemblies include V-cut milling, contour milling, nibbling, UV and heat cure resigns, two-part epoxies, and clip addition.
Additionally, BTI’s unique ability to combine the aforementioned technologies into one fully integrated system enables our clients to reduce capital expenditures, increase product quality, and minimize floor space requirements.
Let our staff of more than 50 engineers design a custom solution for your specific requirements. Furthermore, our commercial Measurement & Testing Services Group (M&T Services) can assist with everything from prototype testing and R&D work to master certification and running small-to-medium production runs.
If you don’t see the product you are looking for, or have specific questions, please contact us.