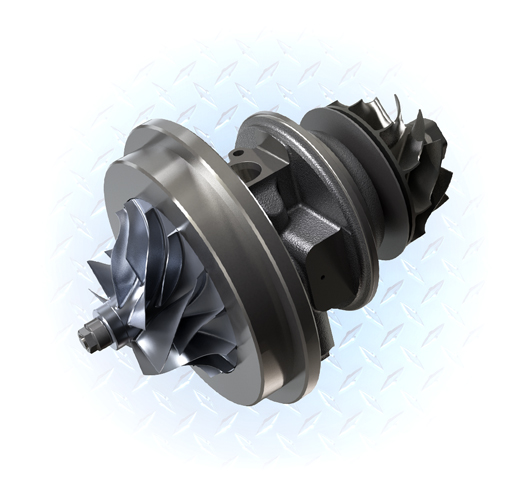
BTI engineers and manufactures a complete line of manual, semi-automatic, and fully automatic precision measurement and testing equipment for all turbo charger components and complete assemblies
BTI engineers and manufactures a complete line of manual, semi-automatic, and fully automatic precision measurement and testing equipment for all turbo charger components and complete assemblies (CHRAs). Traditional equipment for this application includes balancing equipment, dimensional gages, mass centering equipment, eddy current crack detection systems, surface finish/oxide measurement equipment, NVH equipment (noise, vibration, and harshness), functional test stands, resonant frequency measurement systems, specialized test systems, and destructive testers. Equipment layouts vary to accommodate any production rate. Typical correction methods for balancing include drilling, center drilling (mass centering), milling, and grinding.
Additionally, BTI’s unique ability to combine the aforementioned technologies into one fully integrated system enables our clients to reduce capital expenditures, increase product quality, and minimize floor space requirements.
Let our staff of more than 50 engineers design a custom solution for your specific requirements. Furthermore, our commercial Measurement & Testing Services Group (M&T Services) can assist with everything from prototype testing and R&D work to master certification and running small-to-medium production runs.
If you don’t see the product you are looking for, or have specific questions, please contact us.